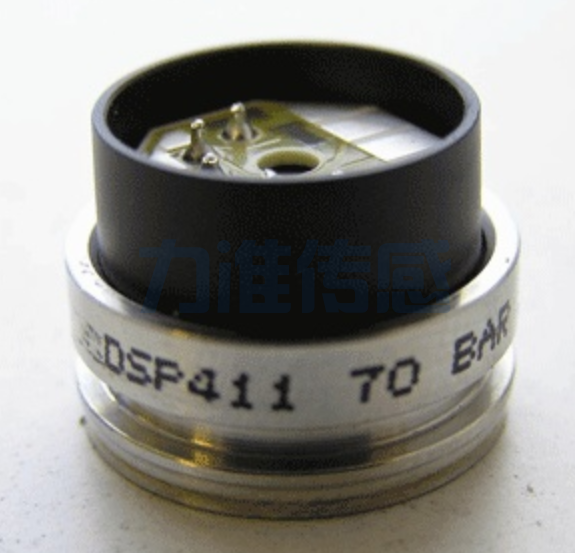
以往,使用硅敏感元件的油壓傳感器在測試性能和可靠性時,會受到多種因素的影響。不過,目前上市的最新版本得益于許多機械設計的改進,因此能夠克服這些缺點。
大部分硅壓敏元件是介質隔離型的,也就是說,他們使用隔離隔膜來工作.當測量壓力時,隔膜會通過油液彎曲壓力傳給硅片。傳統的充油隔膜、硅壓力傳感器比最新的傳感器所使用的油量要大得多。
盡管用戶通常不關心這種油的價格,但是它對傳感器的總體性能和熱穩定性的影響是一個關鍵的設計因素。按照傳統的設計,空氣會滲透到房子里,然后陷入石油中,這樣就會產生問題。油品的物理性質隨空氣的膨脹和收縮而變化,當傳感器的工作溫度波動時,會引起測量誤差。當傳感器變得不那么密封,更多的空氣將進入室內,隨著時間推移,問題會惡化。
為解決這些問題,最新的硅壓敏元件采用了改進的機械密封設計,與先前的版本相比,它只使用了油箱的一小部分。也就是說,即使空氣進入油中,油的量也會減少,所以溫度波動對油的影響會更小,從而使得測量結果更可靠,熱穩定性也會提高。這一影響并未完全消除,但與傳統版本相比已大大降低。這就是說,最新的傳感器經過改進,可以適用于真空環境下的機械密封。
更高的超壓現在也可能發生。一般來講,最新的硅壓敏元件在1bar以上工作時,會產生5倍的超壓,遠高于目前市場上的產品,因此,即使是在系統超壓狀態下,用戶也可以得到額外的安全保護。類似地,最新的傳感器在低于1巴赫的壓力范圍下可以提供10倍的超壓力,從而保護敏感的低距離隔膜。
與傳統傳感器相比,精度也提高了±0.1%,其中包括分辨率、重復性、熱穩定性等方面的改進,其效果相當明顯。
采用全不銹鋼結構的充油硅壓力傳感器也可用于食品、飲料等。新型傳感器與食品級油配合使用,可抵抗頻繁清洗、化學和其他清潔劑,這是因為密封性能提高了。
以往的充油硅壓力傳感器存在著定位問題。舉例來說,如果工廠對水平位置的傳感器進行4mA的標定,但在應用中,傳感器是安裝在一個角度或稍微偏移的位置,油物理特性的變化(因為重力作用)可能會影響傳感器的測量。最新版的版本中,所用的原油明顯減少,而且沒有受到同等程度的影響,而且地心引力的影響大大降低。
有許多原因導致用戶選擇硅壓力傳感器代替壓力傳感器技術。一些技術優勢如下:
全彈性
采用硅壓敏元件,基底膜片一般由‘n’型單晶層硅制成,彈性可達100%至其斷點。因此硅是一種理想的傳感膜片材料。
小時滯
高彈材料與接近完美的粘結和集成應變計相結合,形成幾乎無滯后的結構。這種方法保證了壓力讀數的準確性,與壓力變化的方向無關。
重復的。
應變儀是把壓力信號轉化為電信號的關鍵部件。因為這兩種量規是化學變化區域的均勻材料,它們幾乎完全變形(沒有滯后或分離現象)和應力隔離。也就是說,在很多壓力循環中,壓力測量的重復性都很好(即傳感器不存在疲勞)。
高規系數
當壓力變化一定時,半導體應變計之間的電壓降可達到較高的水平,這意味著模擬數字分辨率能得到更好的利用,信噪比也能得到改善。
簡潔輕巧。
硅片及硅壓阻元件采用化學腐蝕、微機械加工、摻雜與掩蔽等組合方式,利用微電子元件來制造機械結構,從而制造出微型敏感元件。因為感測膜片通常限制了整個傳感器的設計直徑,一個更緊湊的感測元件可以幫助工程師設計出更緊湊、更輕的壓力傳感器。
加快速度
硅傳感器元件的緊湊和重量減輕意味著它們對加速力的敏感度較低。所以這些傳感器在具有高G力、高振動和沖擊的場合都是首選。
穩定性強
不在感測膜片表面粘貼、印刷或電鍍半導體應變計,而是同一材料的化學變化部分。在使用過程中,應變片鍵會隨壓力和溫度的變化而惡化或改變,從而導致傳感器性能的不穩定。
高超常壓力
半導體應變計比其他類型的應變計具有更高的標準系數,這樣就可以在給定的壓力范圍內使用更硬的膜片,從而能夠指定高超壓等級,但又不會對靈敏度產生太大的影響。硅膠具有較高的彈性,與其他彈性較低的隔膜材料相比,硅膠具有較低的應變能力,應力較小。
動力反應
因應變片具有較高的靈敏度,所以相對于感測膜片的橫截面面積來說,它的厚度更大。另外,小尺寸會產生高的固有頻率。這種彈性與原子結合的應變計,使得硅應變片能對快速變化的壓力作出反應。